Why Superheated Steam?
Using the superheated-steam process is the safest, most cost-effective and thorough method to clean up both bulk and residual quantities of alkali metals.
The advantages:
-
The reaction is extremely controllable and easily stopped in an emergency.
-
When the steam is shut off, the minimal amount of moisture in the gas space is consumed or vented.
-
Response time is typically less than one minute.
-
-
The vessel containing the alkali metal is kept at atmospheric pressure.
-
Actually, the vessel is kept slightly positive (~5"w.c.).
-
There are no pressure “excursions.”
-
-
Reaction end-points are very distinct and readily discernable with a high degree of certainty.
-
When the upper surface of the alkali metal is fully reacted, there is no more live metal.
-
There are no pockets of metal shielded by hydroxides or their hydrates.
-
-
The high temperatures mean that the caustic formed is anhydrous, which provides the following advantages:
-
The anhydrous caustic stays molten (above 605°F), so there are no inclusions.
-
The density of the molten caustic is significantly higher than the alkali metal, so the caustic settles at the bottom of the vessel and the metal stays at the top, continuously exposing fresh surfaces for reaction.
-
Alkali metals are typically not miscible with their caustic reaction products, so there is a distinct interface with the metal on top, making the end-point of the reaction easier to detect.
-
-
High moisture-injection rates mean the alkali metal gets very hot (> 800°F).
-
This assures there is no moisture accumulation either from the steam or hydrate formation.
-
No “rollover” reactions occur because of a spill of hydrated caustic into live metal.
-
The reaction zone is simply too hot for moisture to exist as a liquid.
-
-
Moisture is introduced into the gas space of the vessel; the upper portions and sidewalls of the vessel are exposed to the moisture and cleaned very thoroughly.
-
Metal-free caustic is produced, which can be used as a substitute for commercially purchased caustic.
Easily cleans piping systems in-situ, although careful study and preparation may be required.
-
There are NO POPS, BANGS, OR SUDDEN PRESSURE SURGES.
-
Carbon and stainless steel can be used. Tanks are typically suitable for re-use.
-
Does not add organics, which might have regulatory impacts or introduce additional fire hazards.
-
Does not add any potentially toxic materials to the processing area.
-
Capable of cleaning the following:
-
Reactors and tanks of any configuration
-
Tanks and equipment of extremely complex geometry
-
Cold Traps
-
Valves
-
Heat Exchangers
-
Piping
-
Pumps
-
-
Finally, metal can be reacted at rates of several hundred pounds PER HOUR, meaning the project will be completed quickly.
-
CEI’s processing equipment is fully skid-mounted and takes only about one week to set up.
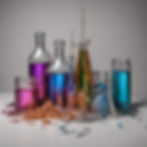
Removal, Cleanup, Disposal of Sodium, NaK, and Alkali Metals
Creative Engineers, Inc. can handle all of your chemical removal, cleanup, and disposal needs with respect to sodium, NaK, and alkali metals. Whether for routine maintenance, decommissioning, or environmental remediation, CEI can provide a complete service.
Operational Temperature vs. Pressure
Can a carbon-steel tank take the high temperatures of superheated-steam cleaning?
Superheated-steam cleaning of alkali-metal tanks has long been a concern because of the high temperatures in the liquid pool. Tanks are normally designed for a pressure-and-temperature limit that does not anticipate temperatures as high as 1200°F.
CEI has been cleaning tanks with large quantities of alkali metals for many years and never experienced a problem, principally because the process is run at essentially zero pressure. To help potential customers understand that the process can be done safely, CEI commissioned a Licensed Professional Mechanical Engineer with pressure-vessel design experience to tell it what the ASME-code calculations would predict for an allowable operating pressure under various scenarios.
In all cases, it was determined that the allowable pressure was higher than the 0–1 psig that CEI’s system would place on the tank. Remember that the advantage of the superheated-steam process is that the large “excursions” that happen with WVN do not happen with superheated steam.
Here are a couple of examples to help illustrate the point.
Caustic Stress Corrosion Cracking
Based on its operational experience, review of available literature, and discussions with several knowledgeable individuals, CEI believes that there is not a significant threat of metal failure when implementing the superheated-steam process on CS and SS tanks and systems, because the caustic that will be formed will be anhydrous and the operating temperature will be above the caustic-embrittlement danger zone.
Caustic stress corrosion cracking (CSCC) is a failure mechanism affecting both the carbon and austenitic stainless steels. For CSCC to cause a failure, a number of factors and conditions must be present in the correct amounts.
These are:
-
Stress in the metal above some level (generally undefined)
-
Presence of caustic in a specific range of concentrations
-
Temperature in a specific range
-
Exposure time
-
Moisture (in order to have an aqueous system)
These factors are all interrelated.
CEI is aware of two sources of information about CSCC as might be applicable in alkali-metal cleanup projects.
-
General literature
-
CEI’s operational experience in applying the high-temperature, superheated-steam processing for CS and SS tanks, piping, and drums
The two most often referenced articles are “Corrosion in Caustic Solutions” by the Hendrix Group and “Metallurgical Problems Associated with Large Sodium Loop Operations” by N. Hoffman. These articles cover only a portion of the potential conditions that may be present in the application of superheated steam to clean alkali metal containing parts.
The temperature and caustic-concentration conditions present during the reaction of pools of metal with SHS are not addressed by these articles. No data have been found by CEI, or provided to CEI by industry contacts, that address CSCC at very high temperature and anhydrous conditions. Since the two situations—wetted parts vs. pools—are distinct, they will be treated separately.
Alkali-Metal Clean-up
Collectively, CEI’s principals have more than 150 years of experience working with alkali metals, including sodium, potassium, cesium, lithium, and alloys of these metals. These unique materials require special skill and precautions when cleaning systems involved in their use. Whether the cleaning is for maintenance, decommissioning, or after a spill or accident, CEI has the experience and a well organized process to analyze the project and do the job safely.
Recycling is always a preferred option to disposal, and CEI has the capability to remove and re-use sodium if it is still of commercial quality. CEI has recovered thousands of pounds of sodium and converted it into sodium dispersion, avoiding the generation of waste. The value in recycling is not in the value of the sodium but in the avoided cost of disposal.
When the sodium, potassium, or other alkali metal is not of commercial quality, disposal becomes necessary. CEI’s engineers have the knowledge, skill, and experience to safely react the metal to a hydroxide, which can then be removed easily from the tank, piping or other components. For more info on disposal, go to our remediation section.
Following conversion and removal of the hydroxide, the system can be flushed with water to remove residual hydroxide and make removal safe.


Remediation
Creative Engineers, Inc. specializes in removal of alkali metals from tanks, piping, cold traps, and other components. Sodium, potassium, lithium, and various alloys such as NaK present a significant hazard to clean up. A number of processes have been developed over the years, but only one promises to clean up both large and small quantities in a controlled manner.
The list of potential processes includes:
-
Superheated Steam (SHS)
-
Water Vapor Nitrogen (WVN)
-
Water sprays (only in very rare situations)
-
Water filling (only in very rare situations)
-
Dissolving the residues in ammonia
-
Alcohol washing
-
Flowing a solvent with a reactant (alcohol) through the system weathering
Proper technique selection is generally driven by safety considerations. CEI evaluates each situation using our proven process for the best approach and the unique hazards involved. Each system will be evaluated with regard to:
-
How well it can be drained
-
Disposition of removed sodium
-
Whether or not the tank or system can be cleaned in place
-
Advantages of removing the equipment for cleaning
-
Cleaning technique to be applied
-
Whether or not the system will be re-used
-
Final disposition of system and components
-
Safety and radiological requirements
CEI has a working knowledge of all the processes above for sodium, potassium, and/or NaK. Through more than 30 years of regular hands-on experience, CEI’s staff has come to believe that the superheated-steam process is best. This endorsement of one particular process is not taken lightly, because the clean-up projects typically involve CEI’s owners actually running the process. They are personally at risk and go to extreme lengths to prepare systems and procedures to ensure the safety of their crews, the customer’s equipment, and themselves.
Case 1
50,000-gallon vessel rated at 50 psig at 300°F constructed at SA 516 Gr 70 Carbon Steel, FD head, 0.25-inch-thick plate, 12' dia. by 56' straight side.
Allowable pressure at 300°F = 59 psig
Allowable pressure at 750°F = 44 psig
Allowable pressure at 1000°F = 7 psig
This shows that CEI can implement the superheated-steam process on a carbon steel tank up to 1000°F without exceeding the pressure capability of the tank, even using the conservative calculations of the ASME Pressure Vessel Code.
Case 2
50,000-gallon vessel rated at 45 psig at 300°F constructed at SA 240 (316 SS), FD head, 0.25 inch thick plate, 12' dia. by 56' straight side.
Allowable pressure at 300°F = 46 psig
Allowable pressure at 750°F = 35 psig
Allowable pressure at 1000°F = 33 psig
Allowable pressure at 1400°F = 7 psig
This shows that with a SS tank, CEI can safely implement the superheated-steam process up to our typical 1100°F with no concerns about exceeding the pressure capability of the tank.
Note: These calculations are for a given tank configuration. The design of your tank can be easily reviewed in the same manner to set the upper bounds of the superheated-steam process for your tank.